Page 8 of 10
Re: Progress Update
Posted: Wed May 10, 2017 2:26 pm
by orchardair
Just to show that I am not 100% lazy or anything, here is the next step - welded (although not very pretty):
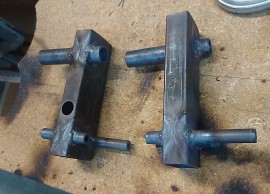
- welded the tubes
- 1494379763623 (1).jpg (19.36 KiB) Viewed 4831 times
Next will be cutting the excess metal, and shortening the tubes to required length.
Re: Progress Update
Posted: Thu May 11, 2017 11:51 am
by orchardair
Much lighter now...
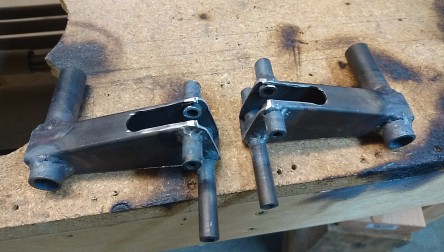
- Still needs tubes trimmed to final length
- metal removed.jpg (37.94 KiB) Viewed 4824 times
The one edge of the (rectangular tube) pieces which is laying on the bench is sometimes shown as being metal. In my case it is air. I did not weld anything on that edge - just removed a bunch of metal.
Since the longer of the two 3/8" tubes goes all the way through the rectangular tube, I figured it is sturdy enough for this non-structural part.
In other words - I added lightness.
Re: Progress Update
Posted: Tue May 23, 2017 3:32 pm
by Bitshifter
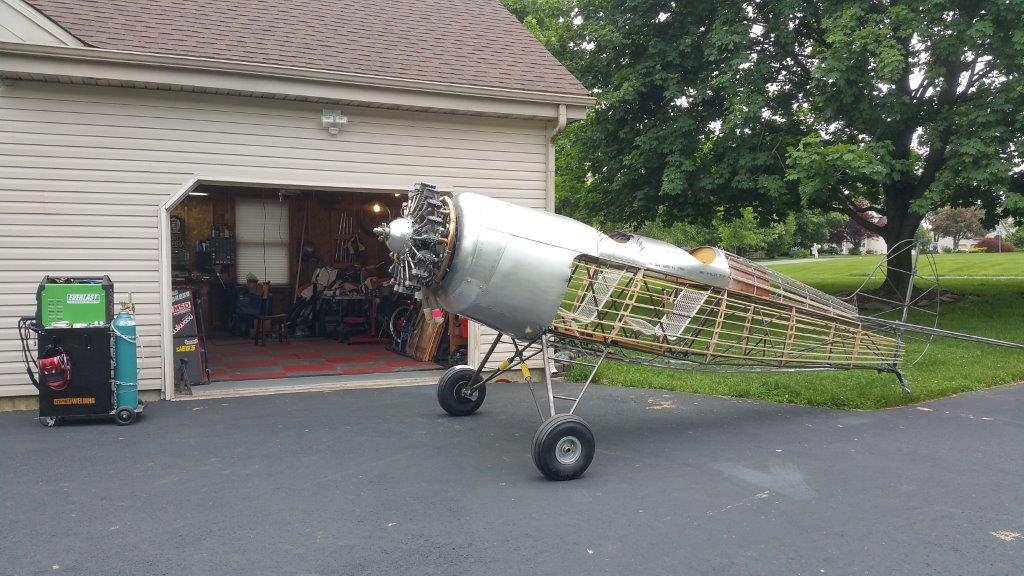
- 20170520_165508.jpg (123.11 KiB) Viewed 4809 times
I needed to throw in a progress update since I finally got it pushed out of the garage.
Re: Progress Update
Posted: Tue May 23, 2017 8:41 pm
by 1964m20e
looking good
Re: Progress Update
Posted: Thu May 25, 2017 10:44 am
by HC85
NICE!!!
I love it!
Looking forward to the day when my ship is at that level of completion!
Re: Progress Update
Posted: Wed Jul 12, 2017 5:29 pm
by orchardair
What a beauty!
Re: Progress Update
Posted: Tue Jul 18, 2017 1:01 pm
by orchardair
One of my "How did you ..." pictorial essays.
This time, perpendicular tube-in tube with doublers. This is used several times in the Hatz Classic. Specifically in this case I am working on the landing gear parts.
Step 1:
I drill the hole for the bushing tube
before I cut the long tube to length. This gives me freedom to drill wherever the drill bit hits the tube. Also leave enough length (1/2" ?) at the short side of the tube beyond the hole, to make things easier.
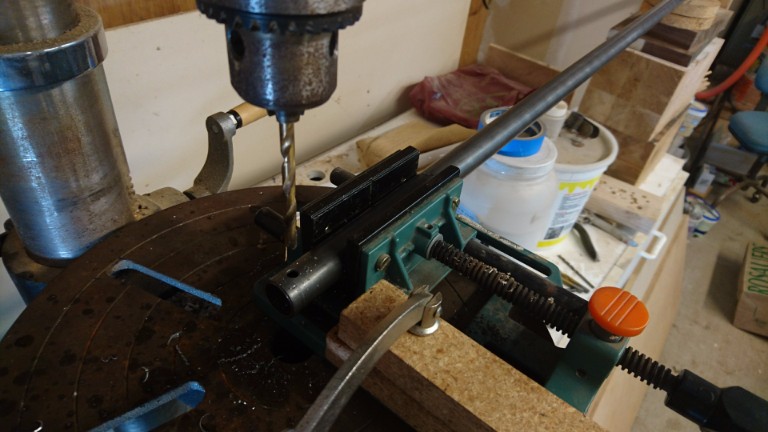
- Drill pre-cut.jpg (76.88 KiB) Viewed 4701 times
Step 2:
Cut the bushing tubes over-sized, ream the hole, cut the long tube to size (measure twice!).
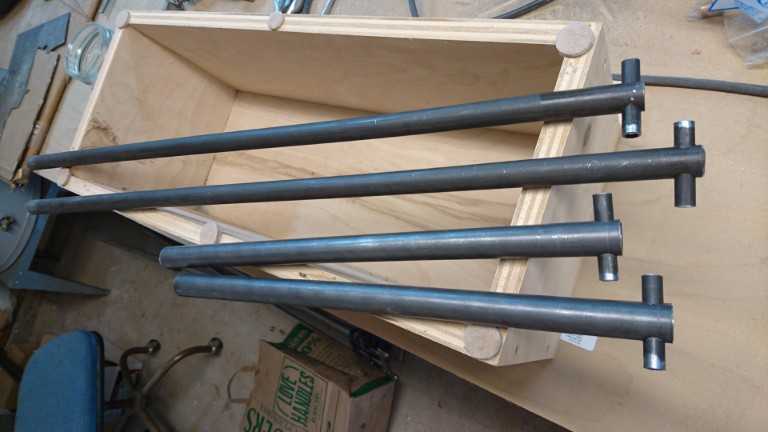
- Cut to length.jpg (70.55 KiB) Viewed 4701 times
Step 3:
Tack-weld the bushing, but only on the part that won't be cut off (see later).
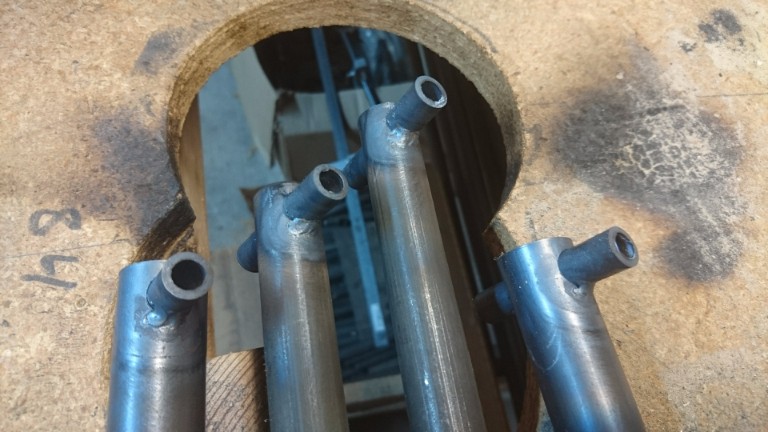
- Tack weld.jpg (86.17 KiB) Viewed 4701 times
Step 4:
Using a combination of angle-grinder, bench grinder, jedi-force and any other trick you have, cut the long tube to shape.
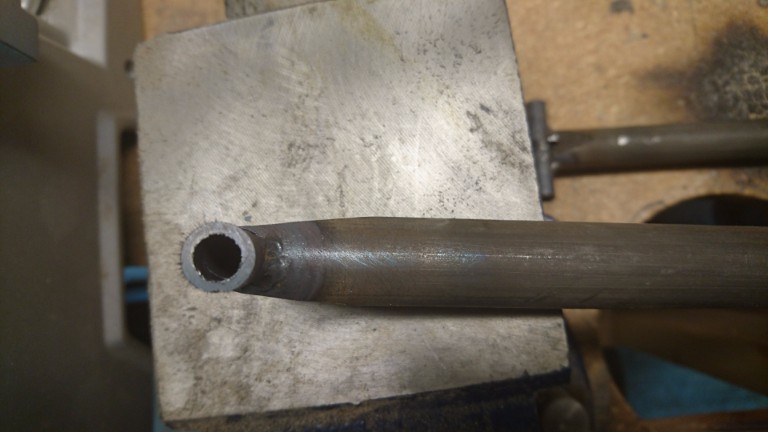
- Shape.jpg (56.23 KiB) Viewed 4701 times
Step 5:
Prepare the doublers. In this case I don't think these are on the files you can download for your waterjet cutter. I just used my angle grinder to cut them from 0.050 sheet, finished on the sander.
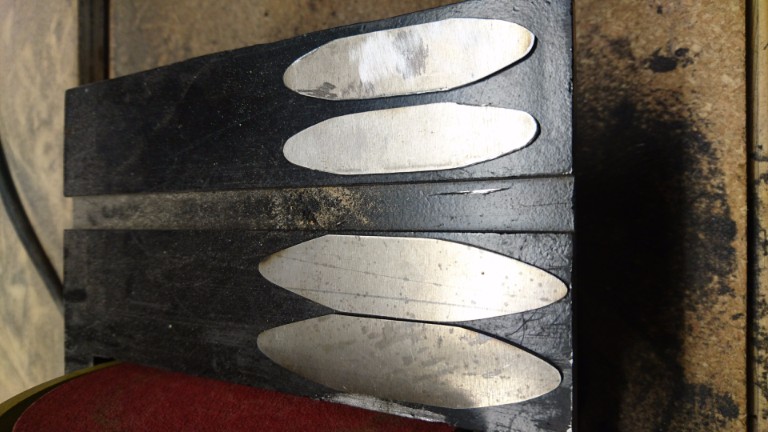
- Doublers.jpg (80.55 KiB) Viewed 4701 times
The next few steps will be in a separate post. I guess there's a limit to how many pictures or size a single post can have.
Re: Progress Update
Posted: Tue Jul 18, 2017 1:03 pm
by orchardair
...(continued)
Step 6:
Position and tack-weld the doublers.
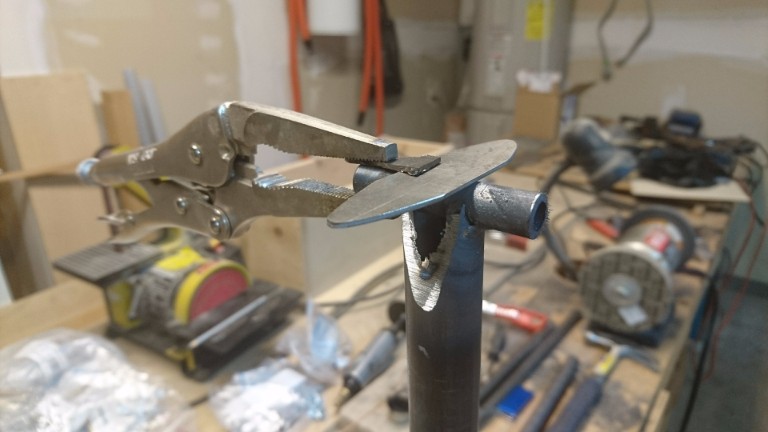
- Tack Doubler.jpg (58.16 KiB) Viewed 4701 times
Step 7:
Heat and bend the doublers.

- Heat bend.jpg (84.8 KiB) Viewed 4701 times
Step 8:
Ready to weld around the doubler.

- Ready to weld.jpg (74.57 KiB) Viewed 4701 times
Re: Progress Update
Posted: Tue Jul 18, 2017 9:03 pm
by mmarien
Nice. I haven't started on the metal other than the compression tubes but there is nothing better for building confidence than someone else making it look easy.
Re: Progress Update
Posted: Wed Jul 19, 2017 10:22 pm
by orchardair
Here ya go, welded all around:
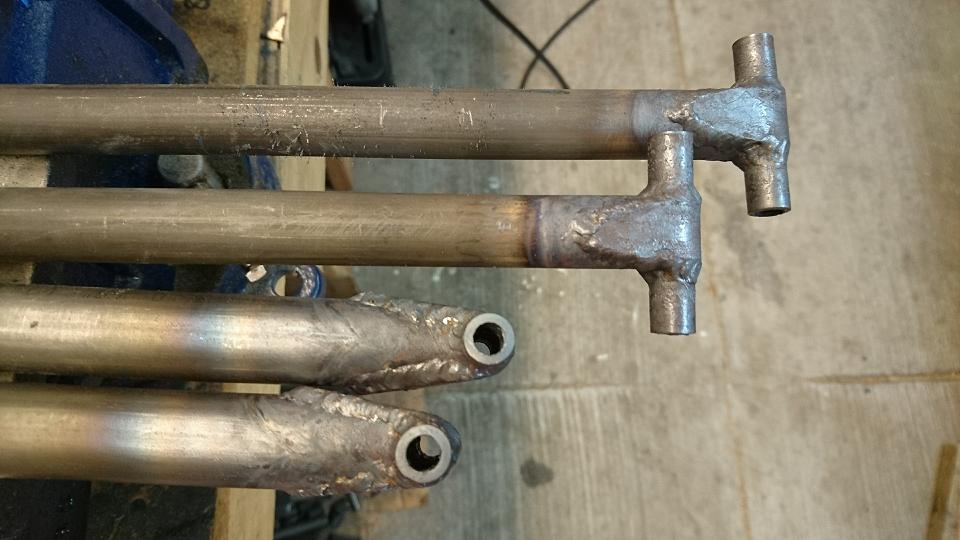
- DSC_1868.jpg (90.56 KiB) Viewed 4690 times
Need to ream the small tubes to 5/16", shorten them to the correct length and drill the holes in the longer tubes.